JHY PCB Blog Hub
Your Source for Expert PCB Design, Manufacturing, and Assembly Insights – Stay Informed with 2025 Trends!
5 Secrets to Choosing the Best Flexible Pcb Board for Your Projects
When embarking on a project that requires advanced electronic components, selecting the right Flexible Pcb Board is paramount to achieving optimal performance and reliability. In a world where technology continues to evolve at a rapid pace, understanding the nuances of flexible printed circuit boards can make a significant difference in the success of your project. With a focus on quality and the assurance that you are choosing from manufacturers committed to excellence, especially those from China, you can tap into global leading technologies.
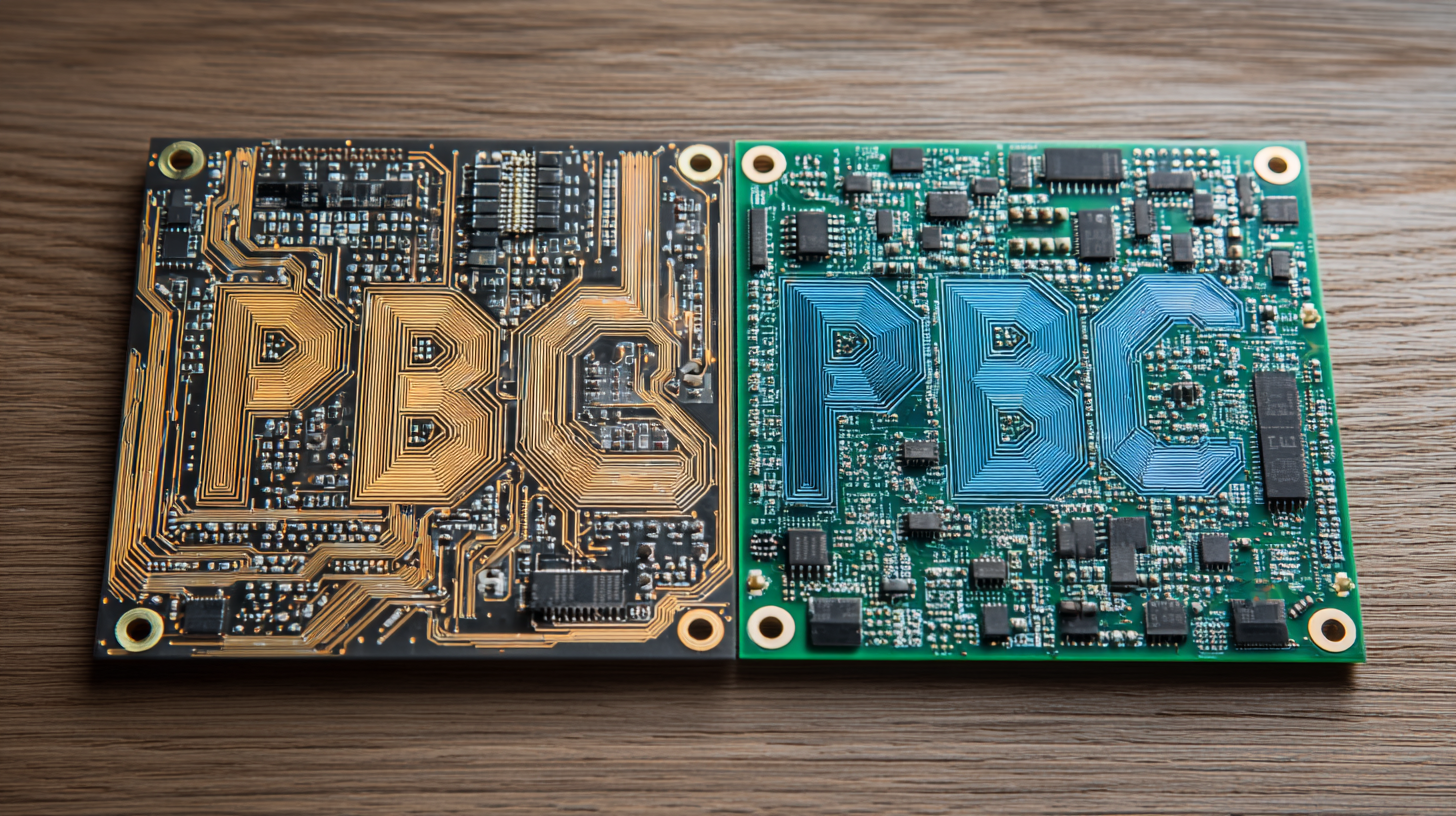
This blog will unveil five secrets that will guide you in making an informed decision when selecting the best Flexible Pcb Board, ensuring not only superior functionality but also compatibility with your project specifications. Join us as we navigate through the key considerations that will set your projects apart in an increasingly competitive landscape.
Understanding the Unique Advantages of Flexible PCB Boards for Modern Applications
Flexible PCB boards have emerged as a vital component in modern electronic applications, thanks to their unique advantages such as space-saving capabilities and lightweight design. According to a report by Research and Markets, the flexible printed circuit board market is projected to reach $25.40 billion by 2025, growing at a CAGR of 10.54% from 2020. This growth is largely driven by the increasing demand for thinner, more compact electronic devices that can accommodate complex circuitry without the added bulk of traditional rigid boards.
One of the most significant advantages of flexible PCBs is their ability to bend and conform to various shapes, which is particularly beneficial in industries like wearable technology and medical devices. A study from IPC indicates that flexible circuits can reduce assembly space by up to 50% compared to standard rigid boards. Furthermore, their enhanced durability allows them to withstand the rigors of dynamic motion, making them ideal for applications that experience constant bending and vibration. These benefits position flexible PCBs as a superior choice for innovative designs and functionality in a wide array of modern electronic applications.
Key Factors to Consider When Selecting a Flexible PCB Manufacturer
When selecting a flexible PCB manufacturer, it’s crucial to evaluate several key factors that can significantly impact the quality and performance of your project. First, assess the manufacturer’s experience and expertise in flexible PCB technology. Look for companies that have a proven track record in the field and can provide references or case studies showcasing their capabilities. This ensures that they are familiar with the complexities involved in producing high-quality flexible PCBs.
Additionally, consider the range of materials and fabrication processes offered by the manufacturer. Different applications might require specific materials, such as polyimide or PET, which have unique thermal and electrical properties. A manufacturer with advanced fabrication techniques, like inkjet printing for flexible sensors, may offer you enhanced customization options and innovation potential.
Finally, it’s essential to evaluate the manufacturer’s commitment to quality assurance and testing. A reliable partner should have robust quality control processes in place to ensure that every PCB meets industry standards and your specific requirements. Regular audits and certifications can also provide peace of mind that the manufacturer adheres to best practices in production.
Material Choices: How to Choose the Right Substrate for Your Flexible PCB
When it comes to selecting the appropriate substrate for your flexible PCB, the material choice is pivotal to ensuring optimal performance and longevity. Flexible printed circuit boards (FPCBs) typically utilize materials such as polyimide and polyester, each offering distinct advantages. According to a report by ResearchAndMarkets, the global flexible circuit market is expected to grow at a CAGR of 10.9% from 2021 to 2026, highlighting the increasing reliance on advanced materials in electronics manufacturing. Polyimide, known for its thermal stability and resilience, is often preferred in applications requiring high heat resistance, making it suitable for aerospace and automotive industries.
In contrast, polyester substrates are more cost-effective and are frequently employed in consumer electronics where flexibility and lower production costs are prioritized. A study by IPC (Institute of Printed Circuits) emphasizes that substrate thickness and dielectric properties directly influence electrical performance, impacting signal integrity and overall design efficiency. By understanding the specific requirements of your project and leveraging insights from industry reports, you can make informed choices that enhance the functionality and durability of your flexible PCBs.
5 Secrets to Choosing the Best Flexible Pcb Board for Your Projects - Material Choices: How to Choose the Right Substrate for Your Flexible PCB
Substrate Material | Key Properties | Temperature Range (°C) | Flexibility | Typical Applications |
---|---|---|---|---|
Polyimide | High thermal stability, excellent dielectric properties | -269 to 400 | Highly flexible | Aerospace, medical devices |
PET (Polyethylene Terephthalate) | Good strength, moderate thermal resistance | -60 to 130 | Moderately flexible | Consumer electronics, automotive |
FR-4 (Flame Retardant) | Cost-effective, good mechanical properties | -40 to 130 | Limited flexibility | Consumer electronics, general applications |
LCP (Liquid Crystal Polymer) | Outstanding electrical performance, high-temperature resistance | -40 to 260 | Very flexible | RF applications, telecommunication |
Teflon (PTFE) | Exceptional chemical resistance, low friction | -200 to 260 | Flexible | High-frequency applications, aerospace |
Design Tips for Maximizing Performance and Durability in Flexible PCBs
When selecting a flexible PCB board for your projects, design considerations play a crucial role in maximizing both performance and durability. One of the primary tips is to prioritize the choice of materials. Using high-quality substrates such as polyimide can significantly enhance the board's thermal stability and mechanical flexibility. This choice will not only improve the board's lifespan but also its ability to withstand harsh environments, making it suitable for a variety of applications in consumer electronics, medical devices, and automotive systems.
Another essential aspect is the layout design. Employing efficient routing techniques and minimizing trace lengths can reduce electrical resistance and electromagnetic interference, which are vital for improving signal integrity. Additionally, incorporating adequate via sizes and placements ensures better connectivity and enhances the board’s overall reliability. Understanding the impact of temperature and moisture on the PCB performance can also guide your design choices; implementing protective coatings can shield the PCB from environmental factors, thereby increasing its durability. By focusing on these design elements, you can create flexible PCBs that not only meet performance expectations but are also built to last.
Cost vs. Quality: Finding the Right Balance for Your Project Needs
When embarking on an electronics project, one of the most critical decisions is the selection of a flexible PCB (Printed Circuit Board). The challenge often lies in striking the perfect balance between cost and quality. While it can be tempting to opt for the least expensive option to keep project budgets in check, this approach may lead to unforeseen complications down the line. Low-cost boards can result in reliability issues, increased failure rates, and ultimately, higher repair or replacement expenses.
On the other hand, investing in high-quality flexible PCBs doesn't imply that you need to break the bank. Understanding your project requirements and the intended application can significantly help in making an informed decision. Look for manufacturers that offer a balance of quality materials, robust manufacturing processes, and reasonable pricing. It’s essential to consider factors such as the board’s expected life cycle, flexibility requirements, and environmental conditions to ensure that your chosen PCB meets all your project needs without excessive costs. By taking these aspects into account, you can achieve a functional and cost-effective design that stands the test of time.
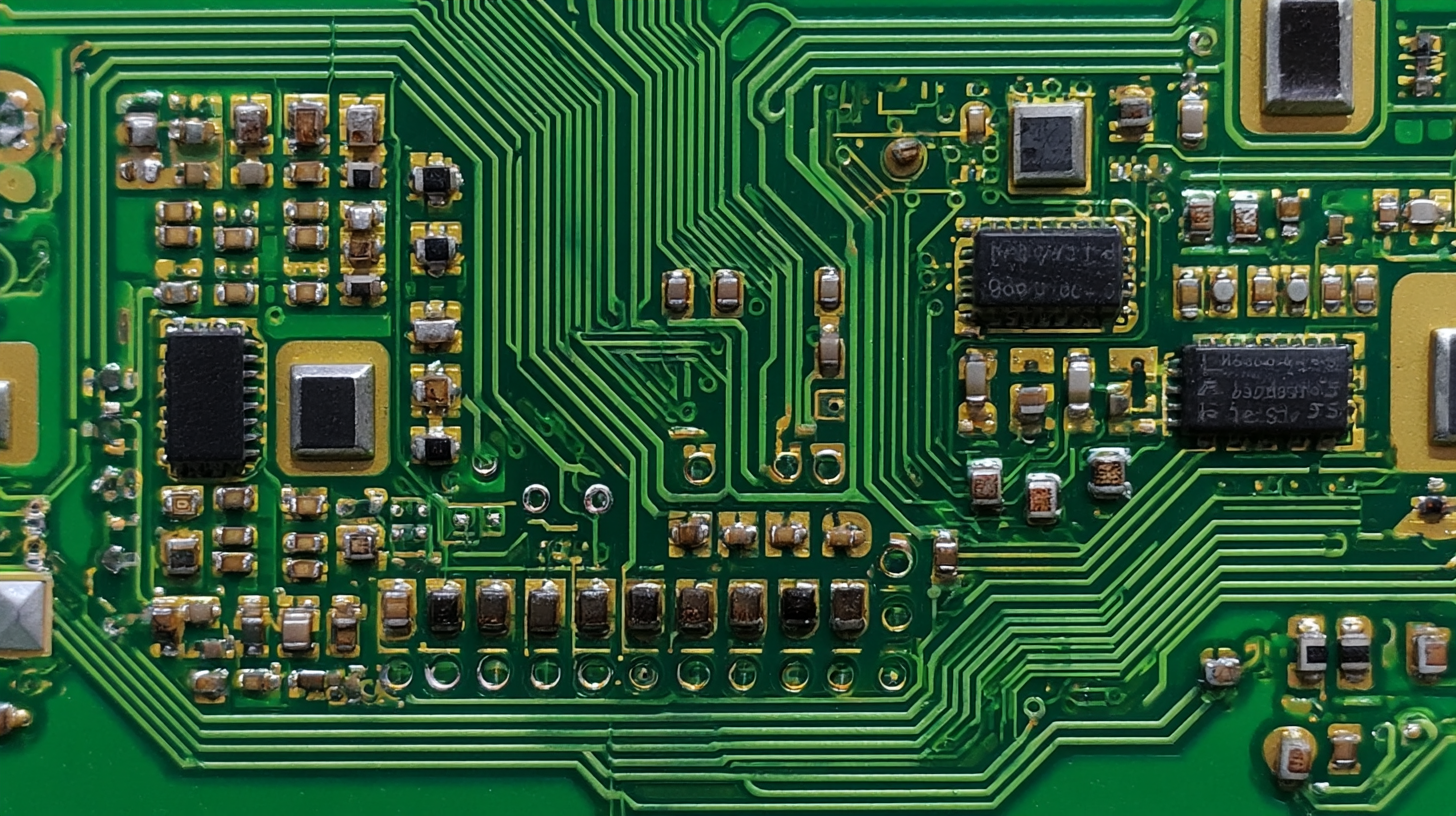